Net-Shaped Manufacturing vs. Traditional Machining for Fasteners: A Comparative Analysis
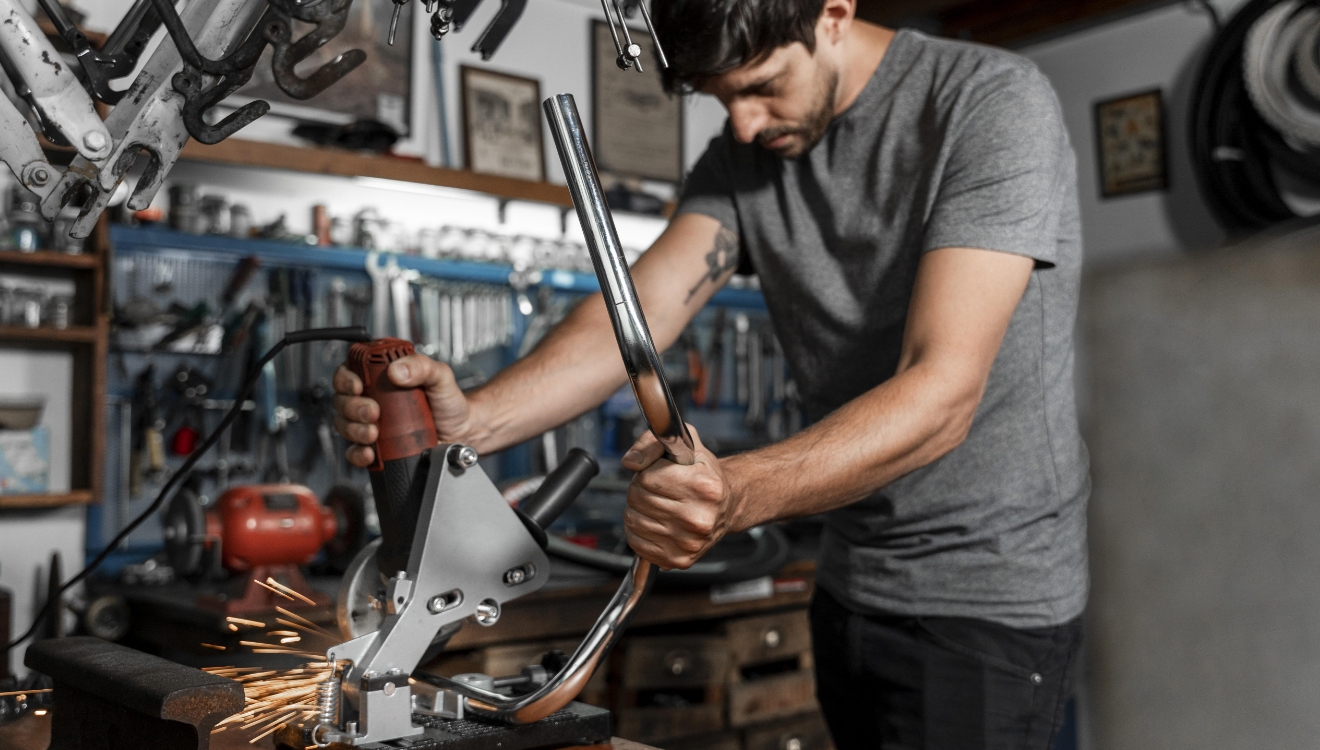
In the rapidly changing manufacturing industry, the focus on efficiency, precision, and cost-effectiveness is crucial. Fasteners, though often overlooked, are vital components used in various sectors, from automotive to aerospace. Understanding their significance helps highlight how they impact product quality and the overall manufacturing process.
This blog offers a comprehensive comparative analysis of two dominant manufacturing techniques for fasteners: net-shaped manufacturing and traditional machining. We will explore their processes, advantages, limitations, and applications, equipping manufacturers with insights to make informed decisions.
Understanding Net-Shaped Manufacturing
Net-shaped manufacturing, also referred to as near-net-shape manufacturing, is a process that produces parts very close to their final shape with minimal need for additional machining. This technique encompasses various methods, including additive manufacturing (3D printing), powder metallurgy, casting, and forging.
Advantages of Net-Shaped Manufacturing
- Material Efficiency: One of the most significant advantages of net-shaped manufacturing is its ability to minimize material waste. Unlike traditional machining, which often involves cutting parts from larger stock materials—resulting in substantial scrap—net-shaped techniques are designed to use only the necessary amount of material. This is particularly advantageous when working with expensive alloys or materials, such as titanium.
- Cost Reduction: By lowering material waste and decreasing the need for secondary machining operations, net-shaped manufacturing can yield considerable cost savings, especially in high-value applications.
- Complex Geometries: Net-shaped processes, particularly additive manufacturing, allow for the creation of intricate designs that would be challenging or impossible to achieve with traditional machining. This capability opens the door to innovative fastener designs that can enhance performance and reduce weight.
- Short Lead Times: The efficiency of net-shaped manufacturing often translates to shorter lead times. With fewer processing steps required, production can be accelerated, allowing businesses to respond rapidly to market demands.
Limitations of Net-Shaped Manufacturing
- Surface Finish: Parts produced through net-shaped methods may require additional finishing processes to achieve the desired surface quality, which can add time and costs.
- Mechanical Properties: The mechanical properties of components made via additive manufacturing or other net-shaped techniques can sometimes fall short compared to those produced through traditional machining.
- Initial Setup Costs: The upfront investment for equipment and technology in net-shaped manufacturing can be high, although it often compensates over time with lower per-part production costs.
Traditional Machining: A Time-Tested Approach
Traditional machining involves subtractive processes where excess material is removed from a solid block to achieve the desired shape. Techniques such as turning, milling, and drilling are staples in fastener production.
Advantages of Traditional Machining
- Precision and Surface Finish: Traditional machining excels in achieving high precision and superior surface finishes, making it ideal for critical components. This level of accuracy is vital in demanding environments where performance is non-negotiable.
- Material Versatility: Machining is adaptable to a wide range of materials. Whether working with metals, plastics, or composites, traditional machining can effectively process various materials, given the right tooling and techniques.
- Established Processes: Many manufacturers are familiar with traditional machining processes, allowing for easy integration into existing workflows. The infrastructure and expertise required for machining are widely available.
- Consistent Quality: The controlled environment of machining operations promotes consistent quality in the final product. Net-Shaped fasteners manufacturer can monitor tolerances closely and adjust processes as needed to uphold quality standards.
Limitations of Traditional Machining
- Material Waste: Traditional machining generates significant waste as material is removed to achieve the final shape. This can be both costly and environmentally unfriendly.
- Longer Lead Times: The multiple steps involved in traditional machining can lead to longer production times, especially for complex components.
- Higher Costs for Small Batches: For low-volume production, traditional machining can be more expensive due to setup and tooling costs, making it less economical for small runs.
Comparative Analysis
When weighing net-shaped manufacturing against traditional machining for fasteners, several factors come into play:
Cost Efficiency
Net-shaped manufacturing tends to be more cost-effective for small batches and complex geometries, thanks to reduced material waste and shorter lead times. Conversely, for large-scale production, traditional machining may prove more economical due to faster cycle times and lower per-unit costs.
Material Utilization
Net-shaped manufacturing excels at utilizing materials effectively, making it the preferred choice for expensive or scarce materials. Traditional machining, while versatile, often results in higher material waste.
Production Speed
Net-shaped manufacturing can significantly reduce lead times by eliminating numerous machining steps. While traditional machining may be slower for complex parts, it can be faster for simpler geometries and high-volume production.
Quality and Precision
Traditional machining offers superior precision and surface finish, critical for high-performance applications. While net-shaped manufacturing is improving in quality, it often requires additional finishing processes to meet stringent standards.
Flexibility and Customization
Net-shaped manufacturing provides greater design flexibility and customization options, enabling the production of complex geometries tailored to specific applications. Traditional machining, while versatile, may necessitate more time and cost to achieve similar results.
Industry Applications
The applications of these manufacturing methods vary by industry. In aerospace, where material properties and precision are crucial, additive manufacturing is gaining traction for producing complex fasteners. Meanwhile, the automotive sector often relies on traditional machining for components requiring precise tolerances and surface finishes. In construction, both methods are utilized, with net-shaped manufacturing increasingly being adopted due to advancements in materials and processes that enhance performance without compromising strength.
Conclusion
The choice between net-shaped manufacturing and traditional machining for fasteners ultimately depends on various factors, including production volume, material considerations, design requirements, and cost constraints. Net-shaped manufacturing offers significant advantages in terms of efficiency, material usage, and design flexibility. In contrast, traditional machining continues to excel in precision, adaptability, and established processes.
As the manufacturing landscape evolves, the potential for hybrid solutions that integrate both methods could emerge, leveraging the strengths of each approach. Manufacturers must remain attuned to these developments to enhance competitiveness and foster innovation in fastener design and production. By understanding the strengths and limitations of each technique, businesses can optimize their production strategies, reduce costs, and improve the quality of their fasteners.
With nearly 82 years of know-how passed from generation to generation, we comprehend the demands of the business. Vico’s progressive engineering capabilities and cutting-edge tooling designs lead to “net-shaped” fasteners. Vico’s assortment of the most accurate, productive and reliable progressive headers includes models made by world leaders such as Asahi Sunac, National Machinery, Sakamura, Nedschroef and Asahi Okuma. These multistation forming machines with 4,5 and 6 forming dies provide us outstanding flexibility with high production abilities. With the means to cut off 15-32mm wire and with forming tonnages up to 550 tons, “Net Shape” designs of even the most highly tolerance precision is realized. Shortened lead times, due to warehoused steel, in house tool manufacturing and a reactive sub-supplier chain make us an appealing option. For more information, please request for a quote.